Soldadura láser
Nos últimos anos, grazas ao rápido desenvolvemento da nova industria enerxética, a soldadura con láser penetrou rapidamente en toda a nova industria enerxética debido ás súas vantaxes rápidas e estables.Entre eles, os equipos de soldadura con láser representan a maior proporción de aplicacións en toda a industria da nova enerxía.
A soldadura con láser converteuse rapidamente na primeira opción en todos os ámbitos da vida debido á súa rápida velocidade, gran profundidade e pequena deformación.Desde soldaduras por puntos ata soldaduras a tope, soldaduras de acumulación e selado, a soldadura con láser proporciona unha precisión e control incomparables.Desempeña un papel importante na produción e fabricación industrial, incluíndo industria militar, asistencia médica, aeroespacial, pezas de automóbiles 3C, chapa mecánica, novas enerxías e outras industrias.
En comparación con outras tecnoloxías de soldadura, a soldadura con láser ten as súas vantaxes e desvantaxes únicas.
Vantaxe:
1. Velocidade rápida, gran profundidade e pequena deformación.
2. A soldadura pódese realizar a temperatura normal ou en condicións especiais, e o equipo de soldadura é sinxelo.Por exemplo, un raio láser non deriva nun campo electromagnético.Os láseres poden soldar no baleiro, aire ou certos ambientes de gas, e poden soldar materiais que son a través de vidro ou transparentes ao raio láser.
3. Pode soldar materiais refractarios como titanio e cuarzo, e tamén pode soldar materiais diferentes con bos resultados.
4. Despois de que o láser estea enfocado, a densidade de potencia é alta.A relación de aspecto pode chegar a 5:1 e pode chegar a 10:1 ao soldar dispositivos de alta potencia.
5. Pódese realizar microsoldadura.Despois de enfocar o raio láser, pódese obter un pequeno punto que se pode colocar con precisión.Pódese aplicar á montaxe e soldadura de pezas micro e pequenas para conseguir unha produción en masa automatizada.
6. Pode soldar zonas de difícil acceso e realizar soldaduras a longa distancia sen contacto, cunha gran flexibilidade.Especialmente nos últimos anos, a tecnoloxía de procesamento con láser de YAG adoptou a tecnoloxía de transmisión de fibra óptica, o que permitiu que a tecnoloxía de soldadura con láser se promocione e aplique de forma máis ampla.
7. O raio láser é fácil de dividir no tempo e no espazo e pódense procesar varios feixes en varios lugares ao mesmo tempo, proporcionando condicións para unha soldadura máis precisa.
Defecto:
1. Requírese que a precisión de montaxe da peza sexa alta e a posición do feixe sobre a peza non se pode desviar significativamente.Isto débese a que o tamaño do punto láser despois do enfoque é pequeno e a costura de soldadura é estreita, polo que é difícil engadir materiais de metal de recheo.Se a precisión de montaxe da peza ou a precisión de posicionamento da viga non cumpre os requisitos, é probable que se produzan defectos de soldadura.
2. O custo dos láseres e sistemas relacionados é alto e o investimento único é grande.
Defectos comúns de soldadura con láser na fabricación de baterías de litio
1. Porosidade da soldadura
Os defectos comúns na soldadura con láser son os poros.A piscina fundida de soldadura é profunda e estreita.Durante o proceso de soldadura con láser, o nitróxeno invade a piscina fundida desde o exterior.Durante o proceso de arrefriamento e solidificación do metal, a solubilidade do nitróxeno diminúe coa diminución da temperatura.Cando o metal fundido da piscina arrefría para comezar a cristalizar, a solubilidade caerá bruscamente e de súpeto.Neste momento, unha gran cantidade de gas precipitarase formando burbullas.Se a velocidade de flotación das burbullas é menor que a velocidade de cristalización do metal, xeraranse poros.
Nas aplicacións da industria de baterías de litio, moitas veces atopamos que os poros son especialmente propensos a producirse durante a soldadura do electrodo positivo, pero raramente ocorren durante a soldadura do electrodo negativo.Isto débese a que o electrodo positivo está feito de aluminio e o negativo está feito de cobre.Durante a soldadura, o aluminio líquido na superficie condensouse antes de que o gas interno se desborde completamente, evitando que o gas desborde e forme orificios grandes e pequenos.Pequenos estomas.
Ademais das causas dos poros mencionadas anteriormente, os poros tamén inclúen o aire exterior, a humidade, o aceite da superficie, etc. Ademais, a dirección e o ángulo do sopro de nitróxeno tamén afectarán á formación de poros.
En canto a como reducir a aparición de poros de soldadura?
En primeiro lugar, antes de soldar, as manchas de aceite e as impurezas na superficie dos materiais entrantes deben ser limpas a tempo;na produción de baterías de litio, a inspección do material entrante é un proceso esencial.
En segundo lugar, o fluxo de gas de protección debe axustarse segundo factores como a velocidade de soldadura, a potencia, a posición, etc., e non debe ser nin demasiado grande nin demasiado pequeno.A presión da capa protectora debe axustarse segundo factores como a potencia do láser e a posición do foco, e non debe ser nin demasiado alta nin demasiado baixa.A forma da boquilla de capa protectora debe axustarse segundo a forma, dirección e outros factores da soldadura para que a capa protectora poida cubrir uniformemente a zona de soldadura.
En terceiro lugar, controlar a temperatura, a humidade e o po no aire no taller.A temperatura ambiente e a humidade afectarán ao contido de humidade na superficie do substrato e ao gas protector, o que á súa vez afectará á xeración e escape de vapor de auga na piscina fundida.Se a temperatura ambiente e a humidade son demasiado altas, haberá demasiada humidade na superficie do substrato e no gas protector, xerando unha gran cantidade de vapor de auga, que dará lugar a poros.Se a temperatura ambiente e a humidade son demasiado baixas, haberá moi pouca humidade na superficie do substrato e no gas de protección, reducindo a xeración de vapor de auga, reducindo así os poros;deixe que o persoal de calidade detecte o valor obxectivo de temperatura, humidade e po na estación de soldadura.
En cuarto lugar, o método de balance do feixe úsase para reducir ou eliminar os poros na soldadura de penetración profunda con láser.Debido á adición de balance durante a soldadura, o balance alternativo da viga á costura de soldadura provoca a refusión repetida de parte da costura de soldadura, o que prolonga o tempo de residencia do metal líquido na piscina de soldadura.Ao mesmo tempo, a desviación do feixe tamén aumenta a entrada de calor por unidade de superficie.A relación profundidade-ancho da soldadura redúcese, o que favorece a aparición de burbullas, eliminando así os poros.Por outra banda, o balance da viga fai que o pequeno burato se balancee en consecuencia, o que tamén pode proporcionar unha forza de axitación para a piscina de soldadura, aumentar a convección e a axitación da piscina de soldadura e ter un efecto beneficioso na eliminación dos poros.
En quinto lugar, a frecuencia do pulso, a frecuencia do pulso refírese ó número de pulsos emitidos polo raio láser por unidade de tempo, o que afectará a entrada de calor e a acumulación de calor na piscina fundida, e despois afectará o campo de temperatura e o campo de fluxo no fundido. piscina.Se a frecuencia do pulso é demasiado alta, provocará unha entrada de calor excesiva na piscina fundida, facendo que a temperatura da piscina fundida sexa demasiado alta, producindo vapor de metal ou outros elementos que son volátiles a altas temperaturas, dando lugar a poros.Se a frecuencia do pulso é demasiado baixa, provocará unha acumulación de calor insuficiente na piscina fundida, facendo que a temperatura da piscina fundida sexa demasiado baixa, reducindo a disolución e escape de gas, o que orixinará poros.En xeral, a frecuencia do pulso debe escollerse dentro dun rango razoable en función do grosor do substrato e da potencia do láser, e evitar ser demasiado alta ou moi baixa.
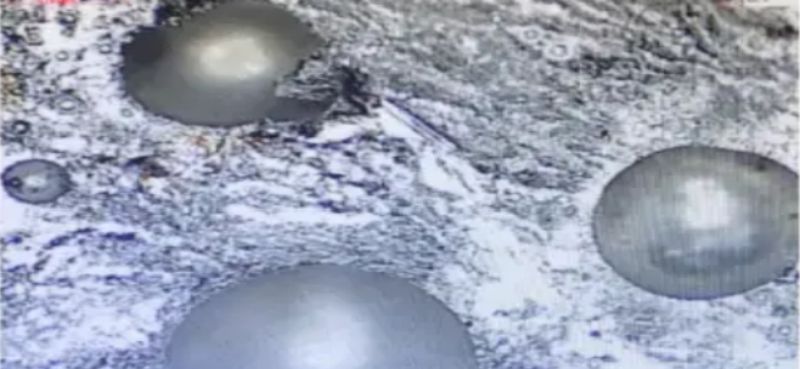
Buratos de soldadura (soldadura con láser)
2. Salpicaduras de soldadura
As salpicaduras xeradas durante o proceso de soldadura, a soldadura con láser afectarán seriamente a calidade da superficie da soldadura e contaminarán e danarán a lente.O rendemento xeral é o seguinte: despois de completar a soldadura con láser, aparecen moitas partículas metálicas na superficie do material ou peza de traballo e adhírense á superficie do material ou da peza.O rendemento máis intuitivo é que ao soldar no modo do galvanómetro, despois dun período de uso da lente protectora do galvanómetro, haberá pozos densos na superficie, e estes pozos son causados por salpicaduras de soldadura.Despois de moito tempo, é fácil bloquear a luz e haberá problemas coa luz de soldadura, o que provocará unha serie de problemas como a soldadura rota e a soldadura virtual.
Cales son as causas das salpicaduras?
En primeiro lugar, a densidade de potencia, canto maior sexa a densidade de potencia, máis fácil é xerar salpicaduras e as salpicaduras están directamente relacionadas coa densidade de potencia.Este é un problema centenario.Polo menos ata agora, a industria non puido resolver o problema das salpicaduras, e só se pode dicir que se reduciu lixeiramente.Na industria das baterías de litio, as salpicaduras son o maior culpable do curtocircuíto da batería, pero non foi capaz de resolver a causa raíz.O impacto das salpicaduras na batería só se pode reducir desde o punto de vista da protección.Por exemplo, engádense un círculo de portos de eliminación de po e tapas protectoras ao redor da parte de soldeo e engádense filas de coitelos de aire en círculos para evitar o impacto de salpicaduras ou mesmo danos na batería.Pódese dicir que a destrución do ambiente, produtos e compoñentes arredor da estación de soldadura esgotou os medios.
En canto á solución do problema das salpicaduras, só se pode dicir que a redución da enerxía de soldadura axuda a reducir as salpicaduras.Reducir a velocidade de soldadura tamén pode axudar se a penetración é insuficiente.Pero nalgúns requisitos especiais do proceso, ten pouco efecto.É o mesmo proceso, diferentes máquinas e diferentes lotes de materiais teñen efectos de soldadura completamente diferentes.Polo tanto, hai unha regra non escrita na nova industria da enerxía, un conxunto de parámetros de soldadura para un equipo.
En segundo lugar, se non se limpa a superficie do material procesado ou da peza de traballo, as manchas de aceite ou os contaminantes tamén provocarán salpicaduras graves.Neste momento, o máis sinxelo é limpar a superficie do material procesado.
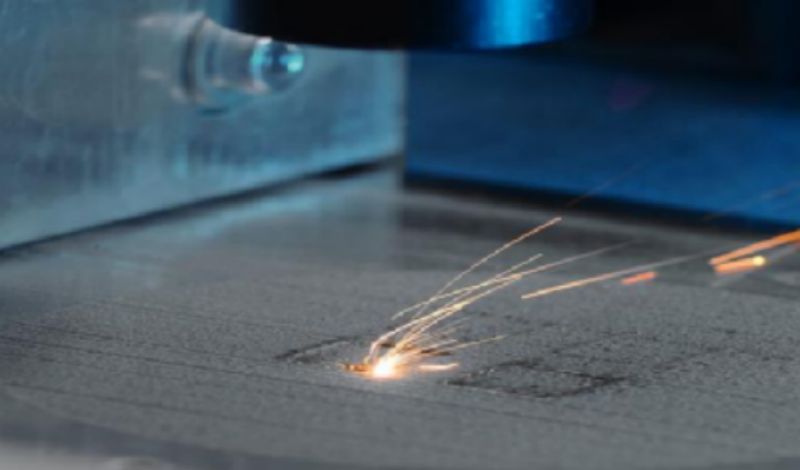
3. Alta reflectividade da soldadura con láser
En xeral, a alta reflexión refírese ao feito de que o material de procesamento ten unha pequena resistividade, unha superficie relativamente lisa e unha baixa taxa de absorción para láseres de infravermellos próximos, o que leva a unha gran cantidade de emisión de láser, e porque a maioría dos láseres úsanse. en vertical Debido ao material ou a unha pequena cantidade de inclinación, a luz do láser que regresa volve entrar no cabezal de saída, e mesmo parte da luz que retorna está acoplada á fibra de transmisión de enerxía e transmítese de volta ao longo da fibra cara ao interior. do láser, facendo que os compoñentes do núcleo dentro do láser continúen a estar a alta temperatura.
Cando a reflectividade é demasiado alta durante a soldadura con láser, pódense tomar as seguintes solucións:
3.1 Use un revestimento anti-reflexión ou trate a superficie do material: revestir a superficie do material de soldadura cun revestimento anti-reflexión pode reducir eficazmente a reflectividade do láser.Este revestimento adoita ser un material óptico especial con baixa reflectividade que absorbe a enerxía do láser en lugar de reflectila de volta.Nalgúns procesos, como a soldadura do colector de corrente, a conexión suave, etc., a superficie tamén se pode gravar en relevo.
3.2 Axustar o ángulo de soldadura: ao axustar o ángulo de soldadura, o raio láser pode incidir sobre o material de soldadura nun ángulo máis adecuado e reducir a aparición de reflexións.Normalmente, que o raio láser incida perpendicularmente á superficie do material a soldar é unha boa forma de reducir as reflexións.
3.3 Engadir absorbente auxiliar: durante o proceso de soldadura, engádese unha certa cantidade de absorbente auxiliar, como po ou líquido, á soldadura.Estes absorbedores absorben a enerxía do láser e reducen a reflectividade.O absorbente adecuado debe seleccionarse en función dos materiais de soldadura específicos e dos escenarios de aplicación.Na industria das baterías de litio, isto é pouco probable.
3.4 Use fibra óptica para transmitir láser: se é posible, pódese usar fibra óptica para transmitir láser á posición de soldadura para reducir a reflectividade.As fibras ópticas poden guiar o raio láser cara á zona de soldadura para evitar a exposición directa á superficie do material de soldeo e reducir a aparición de reflexións.
3.5 Axuste dos parámetros do láser: axustando parámetros como a potencia do láser, a distancia focal e o diámetro focal, pódese controlar a distribución da enerxía do láser e reducir as reflexións.Para algúns materiais reflectores, a redución da potencia do láser pode ser unha forma eficaz de reducir as reflexións.
3.6 Use un divisor de feixe: un divisor de feixe pode guiar parte da enerxía do láser ao dispositivo de absorción, reducindo así a aparición de reflexións.Os dispositivos de división do feixe adoitan estar compostos por compoñentes ópticos e absorbedores e, seleccionando os compoñentes axeitados e axustando a disposición do dispositivo, pódese conseguir unha reflectividade máis baixa.
4. Socavación de soldadura
No proceso de fabricación de baterías de litio, que procesos son máis propensos a causar subcotación?Por que se produce a subcotización?Analizámolo.
Socavado, xeralmente as materias primas de soldadura non están ben combinadas entre si, a brecha é demasiado grande ou aparece a ranura, a profundidade e o ancho son basicamente superiores a 0,5 mm, a lonxitude total é superior ao 10% da lonxitude da soldadura, ou maior que o estándar de proceso do produto a lonxitude solicitada.
En todo o proceso de fabricación de baterías de litio, é máis probable que se produza unha socavación, e xeralmente distribúese na soldadura previa e na soldadura da placa de cuberta cilíndrica e na pre-soldadura e soldadura da placa de cuberta cadrada de aluminio.O principal motivo é que a placa de cuberta de selado debe cooperar coa carcasa para soldar, o proceso de coincidencia entre a placa de cuberta de selado e a carcasa é propensa a ocos de soldadura excesivos, ranuras, colapso, etc., polo que é particularmente propenso a socavacións. .
Entón, que causa a subcotización?
Se a velocidade de soldadura é demasiado rápida, o metal líquido detrás do pequeno orificio que apunta ao centro da soldadura non terá tempo para redistribuír, o que provocará solidificación e socavación en ambos os dous lados da soldadura.Tendo en conta a situación anterior, necesitamos optimizar os parámetros de soldadura.Para dicilo simplemente, son experimentos repetidos para verificar varios parámetros, e seguir facendo DOE ata que se atopen os parámetros adecuados.
2. O exceso de ocos de soldadura, sucos, colapsos, etc. dos materiais de soldeo reducirá a cantidade de metal fundido que enche os ocos, facendo máis probable que se produzan socavacións.Esta é unha cuestión de equipamento e materias primas.Se as materias primas de soldadura cumpren os requisitos de materiais entrantes do noso proceso, se a precisión do equipo cumpre os requisitos, etc. A práctica normal é torturar e vencer constantemente aos provedores e aos responsables do equipo.
3. Se a enerxía cae demasiado rápido ao final da soldadura con láser, o pequeno orificio pode colapsar, provocando un corte local.A combinación correcta de potencia e velocidade pode evitar eficazmente a formación de socavacións.Como di o vello refrán, repite experimentos, verifica varios parámetros e continúa DOE ata atopar os parámetros correctos.
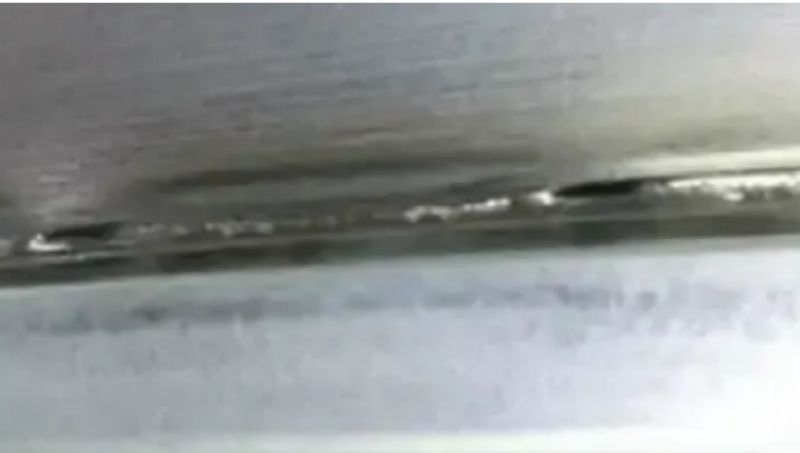
5. Colapso do centro de soldadura
Se a velocidade de soldadura é lenta, a piscina fundida será máis grande e ancha, aumentando a cantidade de metal fundido.Isto pode dificultar o mantemento da tensión superficial.Cando o metal fundido se fai demasiado pesado, o centro da soldadura pode afundirse e formar inmersións e pozos.Neste caso, a densidade de enerxía debe reducirse adecuadamente para evitar o colapso da piscina de fusión.
Noutra situación, a fenda de soldadura só forma un colapso sen causar perforación.Este é, sen dúbida, un problema de axuste de equipos.
Unha comprensión adecuada dos defectos que poden ocorrer durante a soldadura con láser e as causas dos diferentes defectos permite un enfoque máis específico para resolver calquera problema de soldadura anormal.
6. Soldar gretas
As gretas que aparecen durante a soldadura láser continua son principalmente fisuras térmicas, como as fisuras de cristal e as fisuras de licuefacción.A principal causa destas gretas son as grandes forzas de contracción xeradas pola soldadura antes de que se solidifique completamente.
Tamén hai as seguintes razóns para as fisuras na soldadura con láser:
1. Deseño de soldadura non razoable: un deseño inadecuado da xeometría e do tamaño da soldadura pode provocar unha concentración de tensión de soldadura, provocando así gretas.A solución é optimizar o deseño da soldadura para evitar a concentración de tensións de soldadura.Podes usar soldaduras compensadas adecuadas, cambiar a forma da soldadura, etc.
2. A falta de coincidencia dos parámetros de soldadura: a selección inadecuada dos parámetros de soldadura, como unha velocidade de soldeo demasiado rápida, unha potencia demasiado alta, etc., pode provocar cambios irregulares de temperatura na zona de soldadura, o que provoca grandes tensións de soldadura e gretas.A solución é axustar os parámetros de soldadura para que coincidan co material específico e as condicións de soldadura.
3. Mala preparación da superficie de soldadura: non limpar e tratar previamente correctamente a superficie de soldadura antes da soldadura, como eliminar óxidos, graxas, etc., afectará a calidade e resistencia da soldadura e provocará facilmente gretas.A solución é limpar e pretratar adecuadamente a superficie de soldadura para garantir que as impurezas e os contaminantes da zona de soldadura sexan tratadas de forma eficaz.
4. Control inadecuado da entrada de calor de soldadura: un mal control da entrada de calor durante a soldadura, como a temperatura excesiva durante a soldadura, a taxa de arrefriamento incorrecta da capa de soldadura, etc., provocará cambios na estrutura da área de soldadura, o que provocará gretas. .A solución é controlar a temperatura e a velocidade de arrefriamento durante a soldadura para evitar o sobrequecemento e o arrefriamento rápido.
5. Insuficiente alivio do estrés: un tratamento insuficiente de alivio do estrés despois da soldadura producirá un alivio da tensión insuficiente na zona soldada, o que levará facilmente a fisuras.A solución é realizar un tratamento de alivio de estrés adecuado despois da soldadura, como o tratamento térmico ou o tratamento de vibracións (motivo principal).
En canto ao proceso de fabricación das baterías de litio, que procesos son máis propensos a provocar fisuras?
Xeralmente, as gretas son propensas a producirse durante a soldadura de selado, como a soldadura de selado de carcasas cilíndricas de aceiro ou de aluminio, a soldadura de selado de carcasas cadradas de aluminio, etc. Ademais, durante o proceso de envasado do módulo, a soldadura do colector de corrente tamén é propensa. ás fendas.
Por suposto, tamén podemos utilizar fío de recheo, prequecemento ou outros métodos para reducir ou eliminar estas fendas.
Hora de publicación: 01-09-2023